Foaming can be present in many industrial processes like water & wastewater treatment, oil & gas, food & beverage, pharmaceutical, etc. Foam can be an integral part of the manufacturing process or it can be an undesirable side effect. The production of foam can be the source of costly problems such as environmental pollution, reduced yields, production downtime, and cleaning costs in case of overfills.
Excess foam can cause significant damages to equipment such as pumps and filters. So, the use of an accurate and reliable foam measurement technology is needed as it can bring substantial savings to businesses through reduce use of foaming agents, better process control, increased throughput, reduced product losses and fewer equipment failures.
Water & Wastewater
Foaming is present in many water & wastewater treatment processes. For instance, a company in Europe needed to control the level of foam inside a fermentation chamber. Foam level control during biochemical organic decomposition of wastewater is critical to avoid overflow of the fermentation chamber. A laser transmitter was the best choice for this application due to the presence of agitator blades and obstacles inside the tank that made it difficult for other non-contact level technologies.

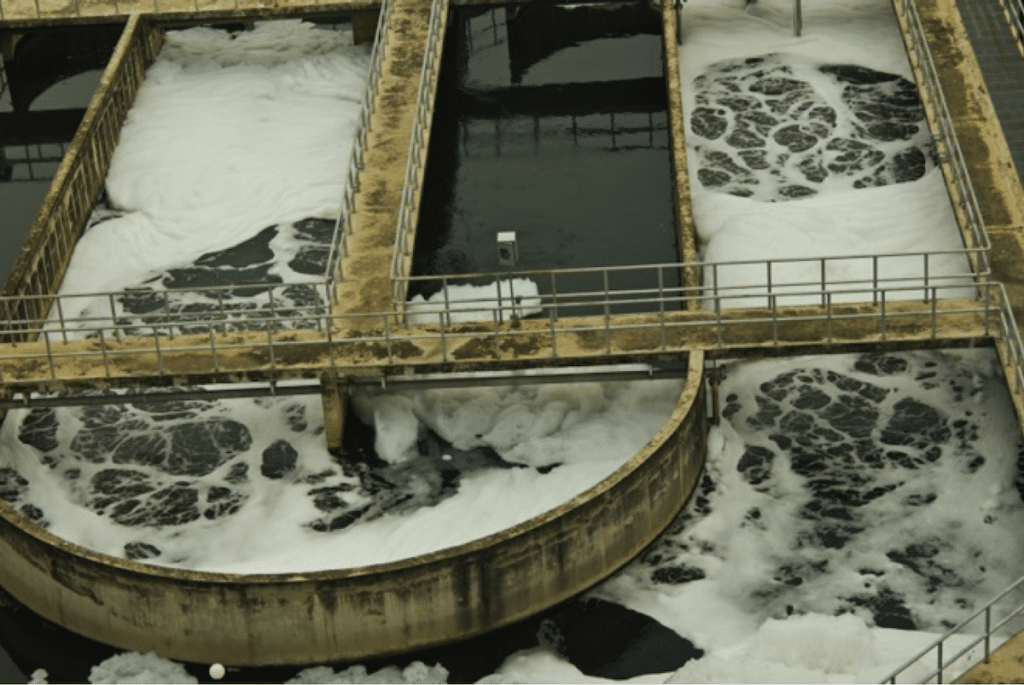
Foaming in activated sludge process is another common operational problem in many wastewater treatment applications. Foaming can occur in aeration tank, secondary clarifier, as well as in digesters. In digesters, foam is always present to some extent and detecting its presence prior to or as soon as it occurs, is important. Our LLT100 was used in such applications to maintain the highest possible level but prevent overfilling due to the growing foam level.
ABB LLT100 is well suited for this application, as it can measure reliably even with changing surface conditions at the different states of fermentation process inside the tank.
Oil & Gas
Foaming may also be an issue in the oil & gas industry. For example, in a Minox deoxygenation system, a knockout pot periodically fills with liquids that can have foam/froth at the top. In this application, it is required to detect the top of the foam to lower the liquid level, so the foam does not get into the blower.
ABB LLT100 laser transmitter is a good candidate for such application as it can reliably measure the level of the top of the foam.
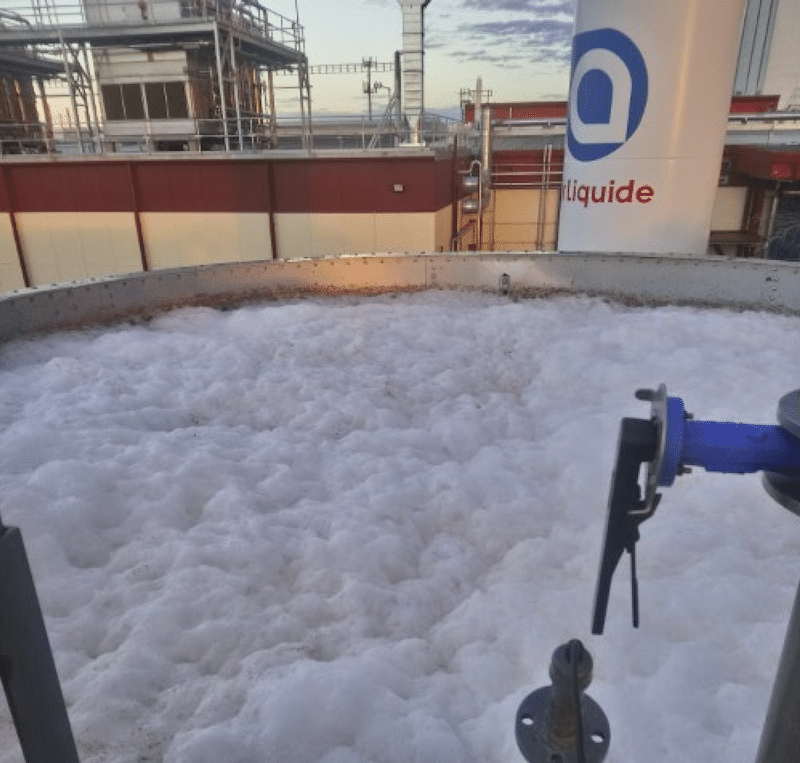
Mining
In the mining industry, floatation cells are used to separate the valuable minerals from ore. The foam is the most precious part of the floatation cells as it contains the precious metals that are then extracted and sent to smelting. Guided wave radars and float-based technologies have been used as a means for overfill protection and to prevent the liquid level from getting higher than the foam level. However, foam level measurement is also critical.
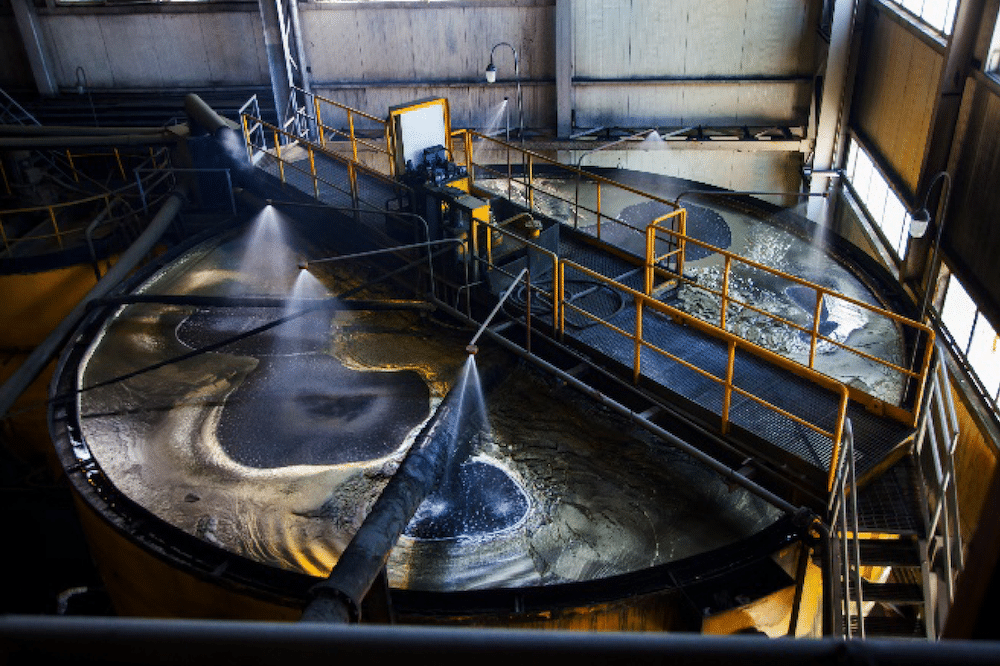
It must not get so high as to overflow, for the foam contains the valuable metals. Furthermore, measuring the height of the foam can help automate the dosage of chemical reagents like sodium cyanide, which is the most important cost item after power consumption in the mining industry. In multistep stepped floatation phases, LLT100 can be used on the first 3 or so units, as the foam thickness can reach 12” or more.
Pulp & Paper
A pulp & paper manufacturer was using defoaming chemicals in a deaerator tank at high dosage level. The customer is using DP for liquid phase and installed an LLT100 to measure and maintain the level of foam at 5%. This helped reduce the amount of chemicals used from 250 cubic centimeter per minute down to 40-60 cc/min leading to cost savings exceeding $100k per year.
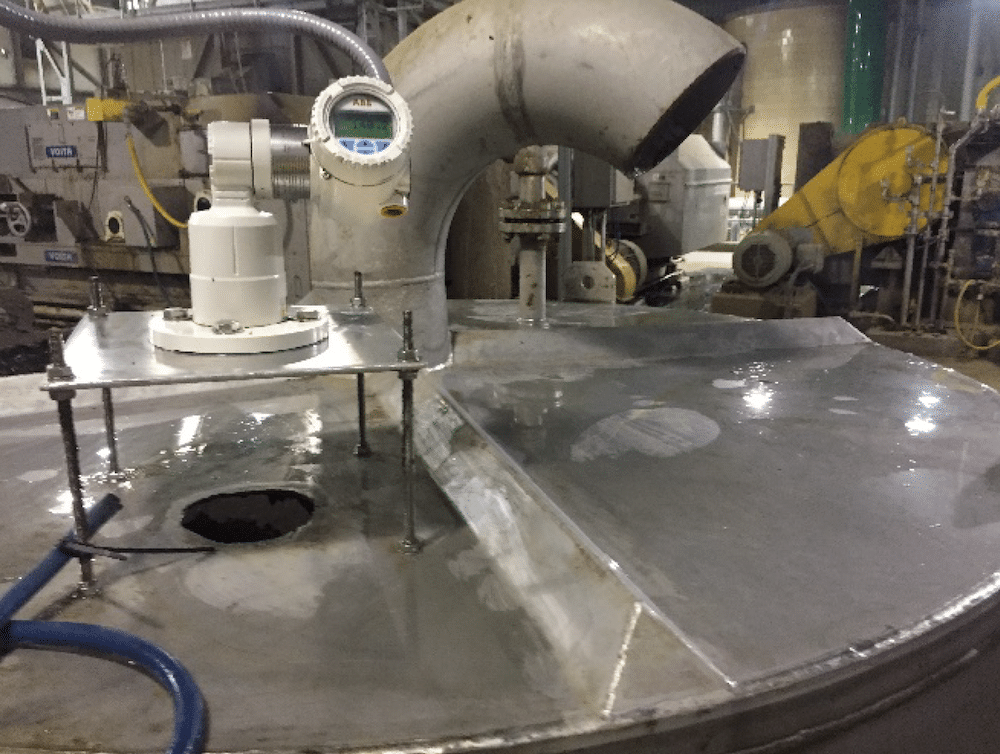
Food & Beverage
Foam level control is a key requirement in the food & beverage industry. For instance, foam is an integral part of the brewing industry. This is particularly true in the fermentation process where substantial foam is created. Level measurement of foam is key to optimize production and prevent costly overflows.
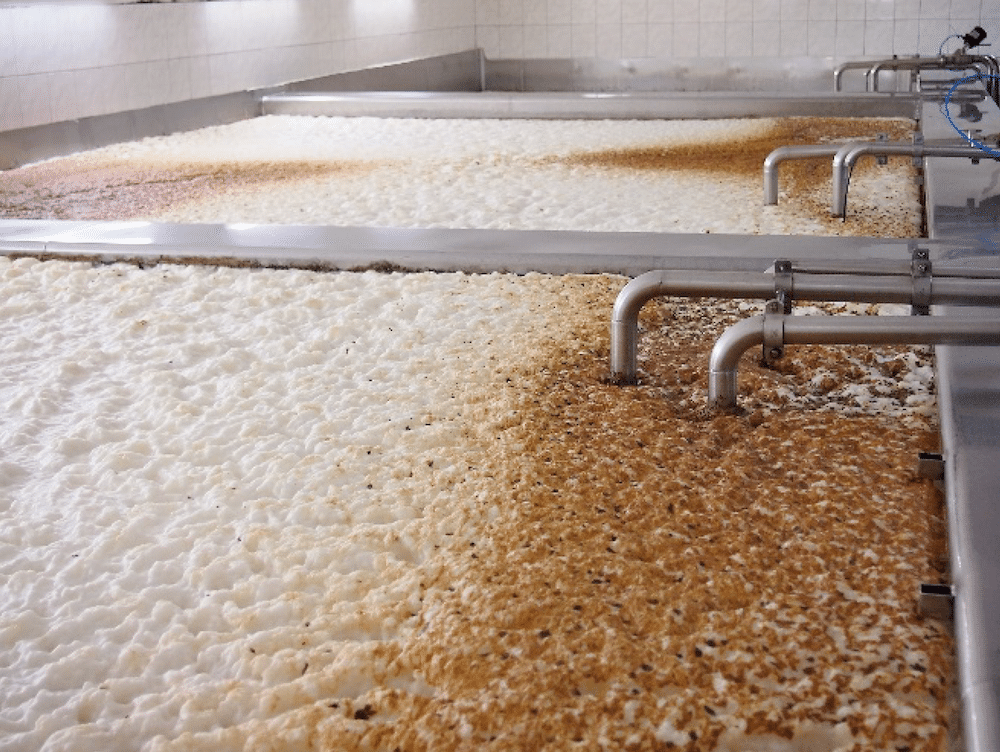
Another application where foam control is important is in the production of sugar from beets and molasse as a co-product. ABB LLT100 Laser transmitter has been used successfully in this application for foam level control and for precise dosing of anti-foaming additives during the production process, resulting in substantial cost-savings. Laser is the best technology to measure the top of dense foam and much more reliable than anything else. Ultrasonic or open-path radars will lose signal from time to time, not the laser.
Pharmaceutical
Crystallization is a separation process very commonly used in the manufacturing of many different materials. It also plays an important role in the pharmaceutical industry, as more than 90% of active pharmaceutical ingredients (API) are synthesized as a crystalline product. Foam is often produced in the crystallization process which then requires the use of antifoam agents or special devices for breaking down the foam.
A pharmaceutical company in Asia has recently upgraded its new manufacturing line of crystallization tanks with stirrer. As part of this upgrade they have required non-contact level measurement. A major challenge of this application was the presence of a stirrer and the narrow space in the tank which made it very difficult for level measurement technologies such as ultrasonic or open path radar. The wide beams of ultrasonic and radar can interfere with the stirrer, side of the tank, or uneven liquid surface, affecting the accuracy of the measurement. ABB LLT100 laser technology was selected because it can work reliably even in tanks with many obstructions and where space is limited.
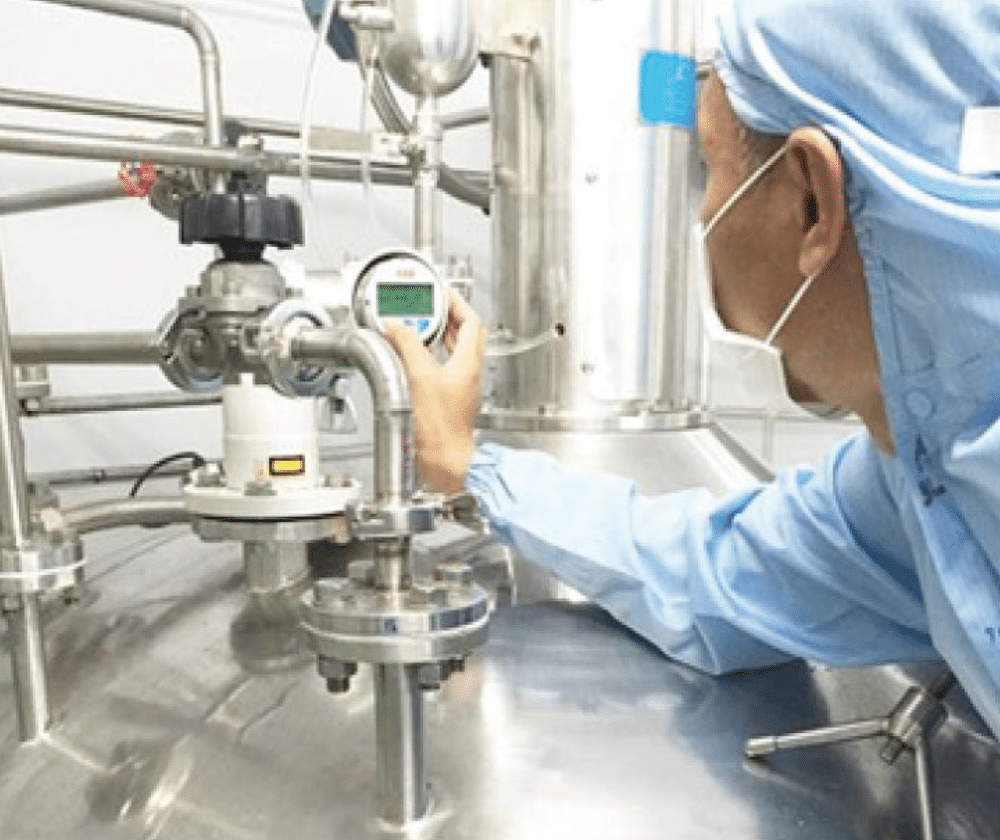
Benefits
LLT100 laser level transmitter presents many advantages for these applications:
- Non-contact technology improving reliability
- Low cost of ownership
- Allows easy setup and offers fast and flexible installation
- Can work with any type of material or surface conditions
- Narrow beam and small divergence
- Can be installed very close to the wall and is unaffected by internal structures or vessel shape
- Reliable even in the presence of agitators or blades
- Can measure reliably the top of dense foam
Conclusion

We have seen that foaming can be present in many industrial processes and can be the source of costly problems such as environmental pollution, reduced yields, production downtime, and cleaning costs in case of overfills. To prevent such undesirable consequences, the use of an accurate and reliable foam measurement technology is needed, and lasers have been used successfully in this application. Laser is the best technology to measure the top of dense foam and it is much more reliable than anything else on the market.
For more information on ABB products please contact us using the form below and a member of our team will be in touch.