The important role of pH measurement throughout chemical processing applications, from production through to effluent discharge, calls for devices that can offer accurate and reliable performance. Nikodem Siwek of ABB Measurement & Analytics explains how developments in digital technology are helping chemical producers to realise new possibilities for improved pH measurement.
From production through to the treatment and discharge of effluent water, being able to accurately measure levels of acidity and alkalinity in chemical production is vital to ensuring the highest standards of product quality, safety and environmental performance. For example, in the electrochemical plating process, an incorrect pH could lead to the peeling of the plate’s surface, degrading the colour and finish.
The pH value of industrial effluent is also significant, as it can lead to serious corrosion in the pipework carrying the waste. Many older chemical and oil processing plant industries will have pipes that are less corrosion resistant and face significant challenges from an imbalance in pH levels. Furthermore, if the pH levels are not correctly balanced at the point of discharge, the damage could also be caused to the aquatic environment, potentially resulting in prosecution and stiff penalties.
The harsh nature of many chemical processes can make life particularly tough for pH sensors. Constantly in contact with the process medium, they are frequently subject to extreme wear and tear that can significantly shorten their service life compared to other types of measurement instruments. For operators requiring high accuracy measurements to ensure the quality of their products, it is important to be able to count on the accuracy of their pH measurement devices and to be able to tackle any potential performance problems before they can develop.
The following looks at how the application of digital technology to pH measurement is helping to achieve this, providing operators with real-time data on process conditions and enhanced diagnostics that can help to warn of potential failures in good time.
Opt for digital
Although many pH sensors still use analogue signals, increasing the latest and most sophisticated sensors are based on digital connectivity. One of the drawbacks of analogue sensors is that they use a high impedance cable, making them susceptible to interference. This can restrict the length of the cable connecting the sensor to the transmitter. With digital pH sensors, the issues associated with high impedance and restrictions on cable length are removed, without compromising accuracy.
In addition to improving productivity by giving a real-time indication of process conditions, online measurement allows the pH sensor to form part of a closed loop control system. Complex algorithms can be incorporated to react to changes in process conditions, adjusting the dosing of chemicals to achieve the desired level. The algorithms can also increasingly predict changing pH levels, enabling corrective action to be taken automatically.
Real time measurement also ensures that the company is not breaching environmental standards, as the pH level is always known and any breaches can be indicated immediately. Digital sensors also allow analysis and signal conditioning to be conducted within the sensor.
Tracking down errors
With large quantities of pH sensors typically being deployed in an application, being able to quickly identify a failing device can help to save both time and engineering resources. Modern digital pH instruments have built in software, making them very quick and easy to install, configure and maintain. It is now increasingly possible to dial into devices and find out everything you need without having to physically visit a device. Many advanced digitally enabled measurement devices will offer sensor checks including internal connections, an indication of sensor memory failure, and an internal electronics check.
One example of a typical fault that affects many pH measurement applications is electrode poisoning. Typically caused by the substance being measured contaminating the reference electrolyte, electrode poisoning can result in erratic and unstable readings that can affect measurement accuracy. Where the substance being measured has a high concentration of ions, contamination can also lead to the reference electrode being attacked, which can quickly lead to a deterioration in performance, and, if not resolved, the eventual failure of the sensor.
Previously, to diagnose whether an electrode had failed, operators would have had to spend time manually checking other possibilities first, such as making sure there is continuity between the reference solution and sample solution and checking that the liquid junction is clean.
With digitalization, the process of diagnosing a fault has now been made much easier, with features such as perpetual impedance diagnostics, which analyses the resistance and impedance between the reference and measuring electrode; and smart reference electrode monitoring, which provides early warning of electrode poisoning, enabling problems to be quickly diagnosed.
Condition monitoring tells more about exactly when to schedule maintenance and allows operators to prepare for it in advance before it can have an impact on the process. By connecting the pH sensor to a digital transmitter, the unit’s data output from its diagnostic functions can be used to accurately determine the root cause of a pH measurement error.
Operators can make use of the increasingly rich data to identify exactly what went wrong and derive strategies or techniques to prevent the same problems occurring in the future.
This enables users to make an informed decision on whether the fault can be fixed or whether the sensor needs to be replaced, minimizing downtime and reducing the need for unnecessary inventory.
Plug and play
The most modern sensors have ‘plug-and-play’ technology, allowing immediate connection of the sensor to a digital transmitter, cutting the time needed for installation and removing any uncertainty during commissioning.
Available in two and four-wire versions, these transmitters combine the latest advances in intelligent sensor diagnostics and management with intuitive HMI operation and a modular design that allows them to be easily upgraded to suit changing requirements. An example is
ABB’s AWT420 four-wire, dual channel transmitter. The transmitter can be used with up to four digital sensors measuring a range of parameters including pH/ORP, conductivity and turbidity. To help simplify operation and maintenance, the transmitter incorporates a range of features including an easily navigable user interface that makes it easy to find and access sensor data and the ability to access sensor information and software updates through a smartphone. To further assist users, the transmitter also includes Bluetooth® technology which can be used in conjunction with a dedicated app to provide up-to-the-minute information and technical support.
The versatility of the unit allows factory-calibrated modules for the different sensor types to be quickly fitted and exchanged using the transmitter’s hinged door, enabling fast and easy upgrading and maintenance in the field. By simply upgrading the transmitter with a new module, operators can avoid the cost and time involved of purchasing and installing new transmitters.
The transmitter also uses a modular approach to integration with different control systems, allowing it to use 4-20mA with HART®, FOUNDATION Fieldbus®, Modbus®, Profibus PA®, and Ethernet communications protocols.
The inclusion of features that help to simplify operation and maintenance enables engineers to quickly and get to the root of any functional issues. For example, many instruments can produce a QR code to indicate faults. Using a smartphone to scan this code gives the technician diagnostics information and the possibility of online help from the vendor. They can quickly discover how to solve the problem and get the pH sensor back in operation as soon as possible.
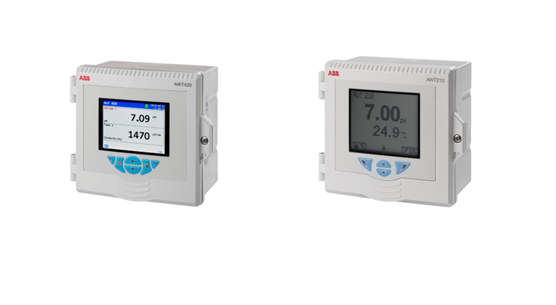
Calibration is key
In treatment processes involving wastewater in particular, failure of an instrument to provide accurate measurement can lead to industrial companies breaching their effluent discharge consent levels, potentially resulting in pollution and, in the worst case, destruction of aquatic environments. As well as running the risk of a potential financial penalty, these types of events can also lead to a damaged reputation. Just like other types of measurement instruments, pH sensors need to be calibrated at regular intervals to ensure they can offer the desired levels of accuracy.
pH probes are dynamic systems and must be calibrated regularly, with the frequency of calibration guided by the application. For a non-critical process application, three- to six-month intervals will typically be sufficient, while more critical or extreme applications would require a higher frequency.
One of the most important aspects of maintaining a pH sensor’s accuracy is calibration with pH buffers. All pH systems, whether analogue or digital, should always be calibrated before use. This requires the pH measurement cell to be calibrated with a solution with a known pH value. However, calibration does have its own peculiarities, being affected by a range of different factors, of which temperature is the most important. Unless the buffer is maintained at an ambient temperature of 25°C, its pH will vary. The pH of a buffer solution that is 9.18 at 25°C, for example, will rise to 9.35 at 10°C.
To compensate, the instrument should be set to the buffers being used. Most modern pH meters will have built-in buffer and temperature tables developed by national standards laboratories and will be able to automatically compensate for temperature variations.
Calibration is achieved by using two different pH standards or buffers or by comparison to a grab sample. It is important to note that in some processes, relying solely on buffers can result in incorrect readings.
Buffer calibration should therefore only be a starting point, followed by one-point grab sample calibrations. In this type of calibration, the sensor is left to acclimatize to the process and a sample is measured with a high-quality lab sensor, with the resulting value being used to calibrate the process pH meter.
Take the strategic view: Maintaining, calibrating, and verifying the performance of pH sensors through digital means is a very good start and can go a long way to achieving an accurate pH monitoring and control process.
Yet, this is only the start. The data available from pH sensors can be combined with that from other instruments to inform decisions across the whole plant and the wider business.
One of the most powerful and effective techniques is to make use of cloud-based infrastructure, which helps more people and systems get access to and act upon the data that is appropriate to their needs. This includes inputs from process-line instrumentation such as pH sensors, as well as signals sent to a range of control and supervisory equipment. These can include elements such as programmable logic controllers (PLCs), supervisory control and data acquisition (SCADA), and distributed control (DCS) systems.
There is also the possibility to make data easier to access and more visible to plant operators and production engineers using customizable dashboards. Displaying key performance indicators on large touch screen displays allows plant operators to be more aware of process variations and respond to them more quickly and effectively. The same data can be run on smartphones and tablets via appropriate apps, making it easier for plant personnel to interact with plant equipment and analytic data.
The main value of digitalization is that it allows a better overview of processes, ensuring decisions are made on a more informed, objective basis. Systems running analytic programs provide insights into key operations such as pH measurement and control. The analysis brings the ability to anticipate changing process trends, deal with potentially anomalous conditions as they occur, and help the organization achieve higher-level operational and business objectives.
Integrating the readings of pH sensors and others into digital management systems makes data collection more efficient, saving both time and costs and making it a more practical way to control overall plant operations. Being able to monitor at a high level in real time, yet still analyse process upsets in greater detail, when necessary, puts plant personnel in a better position to streamline plant efficiency.
Digital techniques are playing an increasing role in all plant applications, not least in the vital monitoring performed by pH sensors. With digital diagnostics, remote verification, and the ability to use their data to inform wider plant operations and business goals, modern pH sensors make a major contribution to plant safety and the highest operational performance.
For more information on ABB products or KC Controls services contact us below and a member of our team will be in touch.
More Articles