In the petrochemical and chemical industries, accurate pressure measurement is paramount to ensure both operational efficiency and safety. Pressure instruments equipped with diaphragm seals often employ devices crucial for disposing residual liquids or trapped gases that could affect pressure measurement. Central to this process are the flushing and drip rings, positioned between a diaphragm seal and the isolation valve, which facilitate the flushing or venting of process media from the face of the seal.
In this blog post, we will explore the main differences between these two types of rings, thereby assisting engineers in making well-informed decisions when incorporating them into their designs.
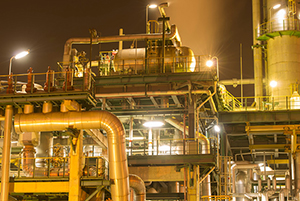
Drip and flushing ring design
Drip rings
Drip rings have a smaller outside diameter than both the process flange and the diaphragm seal flange. Traditionally, they sit on the sealing surfaces of the process valve flange and the diaphragm seal flange, contained within the Pitch Circle Diameter (PCD) of through studding. They are held in position by stud-induced pressure. Additionally, they rely on female NPT threads for their flushing inlet and outlet, necessitating adapters to bring the flushing valves clear of the outside diameter of the flanges.
Flushing rings
Flushing rings have the same outside diameter as the process flange and the diaphragm seal flange, thus allowing flushing valves to be screwed or welded directly onto the outside face. They feature through holes that align with the two flanges, providing centralized alignment and they are typically supplied with pre-fitted ball valves or needle valves for flushing or calibration of the pressure instrument, eliminating the need for NPT threads and sealants.
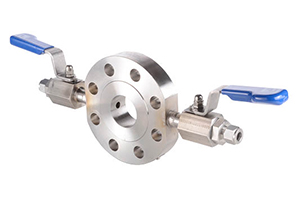
Parker’s extensive range of flushing rings (Image 1) is designed to cater to a variety of flange diameters, accommodating sizes up to 3 inches. An added benefit is the ability to use a smaller process flange with a larger diaphragm seal flange by employing captive studs on both sides of the flushing ring (Image 2). This allows for greater installation flexibility, while also reducing weight and overall costs.
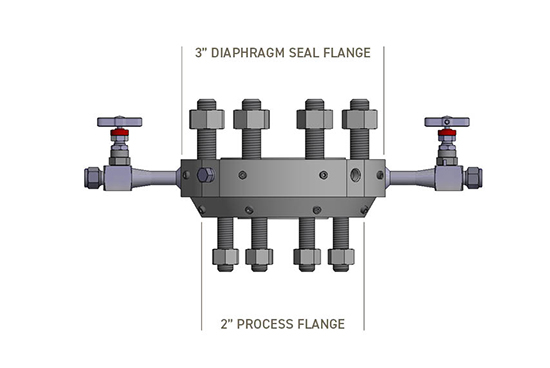
Installation
Drip rings can be time-consuming and inconvenient to install, as they must be held in position by the installer during the process to ensure the right positioning between the flanges. On the other hand, flushing rings are held in place by through-bolts or captive studs, making them easy to install (especially in a non-vertical position). Parker offers captive studding versions with the added benefit of keeping the flushing ring in place if the diaphragm side requires removal. This both simplifies installation and reduces downtime if transmitter removal is required.
Cost
When comparing the costs of drip rings and flushing rings, it is essential to consider not only the standalone purchase price of the items but also the overall cost, which includes the additional components required for installation and the installation process itself. Although drip rings may initially appear to be the less expensive option, the requirement for adapters and valves can significantly increase the total cost. These adapters and valves typically need to be sourced from a different supplier than the drip ring provider. Additionally, they necessitate extra time for assembly and fabrication, either in a workshop or directly on the job site.
Conversely, flushing rings reduce overall costs by eliminating the need for additional adapters since the valves are integrally welded or screwed to the rings. Furthermore, purchasing them from a single supplier means only one order needs to be placed. The streamlined installation process of flushing rings saves time, leading to reduced labor costs. Considering both the component costs and the installation process, flushing rings present a more cost-effective solution for many applications.
Conclusion
In summary, while both flushing rings and drip rings serve similar functions in pressure measurement, there are key differences in terms of design, installation, cost-effectiveness, and maintenance capabilities. By understanding the differences between flushing rings and drip rings, engineers can make informed decisions when selecting the appropriate components for their designs, ultimately improving the efficiency and reliability of their systems.
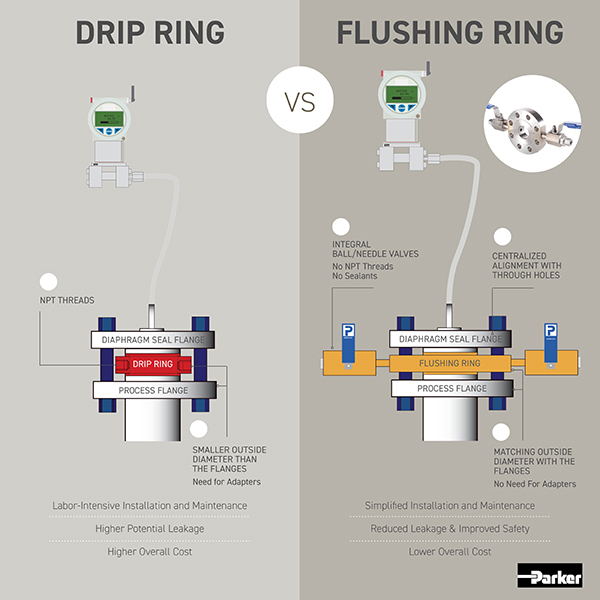