Securing leak-free connection of impulse lines to manifolds for applications that use differential pressure flowmeters is a subject that has taxed instrumentation engineers for more than a century. Back in 1910, when the very first orifice plate installations made an appearance, they involved 33 connections and 16 lengths of tubing! Thanks to the development of highly integrated manifolds, today’s installations often only require just two tube connections. However, ensuring the long-term integrity of these connections remains a contentious issue.
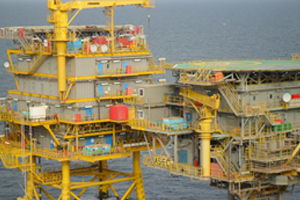
The first manifolds on the market used NPT taper threads for their tube connections. Despite being the bane of installers’ lives, this type of technology continues to enjoy widespread use today, with most manifold manufacturers still offering it as an option. But much better tube connector technologies are now available.
What’s wrong with taper threads?
Unlike compression type tube fittings with one or more ferrules, taper thread fittings rely on the threads themselves to provide the seal. During make-up, progressively larger diameter threads on the fitting are compressed into progressively small diameter threads on the manifold, until eventually there is no clearance left between the crests and roots of the threads and they effectively form a metal-to-metal seal. NPT taper thread fittings are popular because they are relatively inexpensive, but they also have distinct disadvantages. The fittings cannot easily be installed with a specific torque, which makes it all too easy to crack or distort the female part by applying too much torque, or to apply too little, resulting in potential leak paths due to incorrect thread cling. There is also always some thread clearance due to manufacturing tolerances, which means that if the fitting is not tightened to the point where thread deformation creates a metal-to-metal seal, there is a spiral leak path. Furthermore, the upper and lower machining limits of NPT taper threads mean that there might only be two turns of thread engagement in an assembled connection; the most reliable means of preventing this is to use, if possible, a matched pair of male and female parts produced by the same manufacturer.
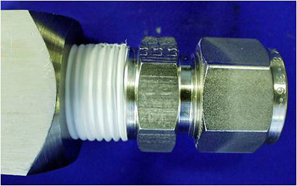
Taper thread can suffer from limited thread engagement
Another major disadvantage of NPT fittings is that their radial orientation cannot easily be adjusted without compromising connection integrity.
Most installers of NPT fittings elect to use some form of thread sealant to help prevent leaks. This usually comprises a fluid carrier which transfers a filler compound into the threads and then cures. Unfortunately, not all sealants act as lubricants and they are also very easy to misapply. Too much sealant can cause system contamination, which can result in unseated valves or blocked lines, while too little can allow the threads to gall (cold weld) during installation, requiring replacement of the entire manifold and tubing system. A further problem is that the fitting cannot be adjusted once the sealant has cured.
A popular alternative approach is to use PTFE tape as a sealant. This additionally acts as a lubricant during assembly and facilitates tighter connection of taper thread fittings – although it can lead to over-torquing. Another issue with PTFE tape is that it has a tendency to shred and cause system contamination. For this reason, its use is often prohibited in sensitive instrumentation systems.
Parker now offers two manifold connection solutions – PTFree connect and inverted A-LOK – which completely eliminate the need for taper threads, PTFE tape and thread sealant.
PTFree connect
Our PTFree connect system provides a simple means of connecting impulse lines to manifolds without involving the use of taper threads, PTFE tape or thread sealant. Available as an option for every type of manifold valve block that Parker produces, PTFree connect offers different versions that accommodate metric tube sizes from 6 to 12 mm and imperial sizes from 1/4 to 1/2 inch.
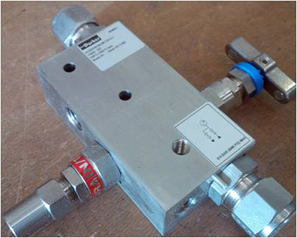
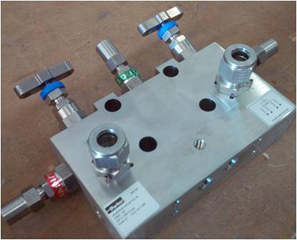
Parker’s PTFree connect system is available on all types of manifold
Manifolds fitted with the PTFree connect system are exactly the same as their standard counterparts, except that their inlet/outlet and drain/test ports can be factory fitted with male adapters, supplied complete with a preassembled nut and ferrule(s). The (parallel) thread on the male adaptor is screwed into the manifold and uses the same type of stainless steel sealing washer as the valve heads, to provide a high-pressure leakproof and bubble-tight connection. The adaptor is securely locked by a cam or locking plate mechanism. We have used this connection principle well over a million times, so you can be confident that it’s a tried and trusted system.
Installation of PTFree connect manifolds is simple. A variety of connection bodies can be used – including straights, elbows, and tees – and all angled components can be freely swiveled to facilitate secure positioning. And if anything does go wrong during installation, the sacrificial element is the male adapter – not the manifold – so the cost of remedial action is considerably less than with any other type of connection.
Inverted A-LOK fittings
More recently, we developed inverted A-LOK fittings, designed specifically for connecting impulse lines directly to manifolds. Like our PTFree connect system, these also eliminate taper threads and the need for PTFE tape or thread sealant, but they do not involve the use of adapters – the tube is fitted directly to the manifold. Each of the two manifold ports forms the female half of a connector and is machined with a cone-shaped orifice and a standard parallel (non-tapered) thread. Each male part comprises a tube and an inverted nut, with threads on its outside surface, which drives two ferrules forward during assembly; the pressure seal is provided by the front ferrule – not the threads of the connector.
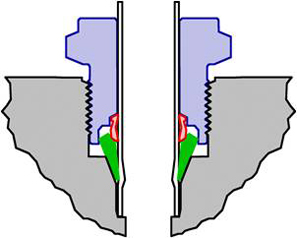
Inverted A-LOK fittings facilitate direct-to-manifold connections
A key advantage of our inverted A-LOK fittings is that the tube is not twisted during installation – all make and remake motion is transmitted axially to the tubing. Since there is no radial movement of the tubing, it is not stressed and its mechanical integrity is not compromised. These fittings are suitable for both thin wall and thick wall tubing, can be used with a wide variety of tubing materials and accommodate repeated disassembly and remake. However, they still require careful installation. If the internal cone becomes damaged, the manifold block will need to be replaced. And due to cross-hole drilling in the block, the technology is not available on all types of manifolds.
For more information on Parker products or KC Controls services contact us below and a member of our team will be in touch.